AVOID INJECTION PLASTIC BLACKENING-LUMINOUS POWDER FOR INJECTION MOLDING
Many of our clients reported to us that when they were trying to add lumous powder in the injection molding production, the plastic products produced became black or dark brown color. Today we will talk about the reasons why this happens and how to avoid this phenomenon.
In the injection molding process, the luminous powder mainly rubs against the metal in the cavity so that the metal chips are mixed into the plastic product, which causes the plastic products to become black.
THERE USUALLY ARE 2 MAIN REASONS FOR INJECTION BLACKING HAPPENS:
1. The proportion of powder is too high:normally should be below 20%.
2. The particle size of the glow in the dark powder is too big: we recommend to use glow in the dark powder particle size of 250 mesh for injection mold as per our experience.
FOLLOW THE STEPS BELOW TO REDUCE THE CHANCE OF HAVING INJECTION BLACKENED PRODUCTS.
PRECAUTIONS FOR LUMINOUS POWDER INJECTION
1. When mixing luminous powder and plastic, it is best to use manual stirring. If you use a mixer to stir, you need to reduce the mixing speed of the mixer, the lower, the better. Unsustainable rotation, the best advice is to use jogging. (The shorter the refueling time, the better)
2. In the injection molding compound, the plastic raw material should match with luminous powder. (If you use luminous masterbatch, the plastic raw material must also be plastic masterbatch; if you use the luminous powder, the plastic raw material must also be plastic powder )makes it easier to mix uniformly, and the dispersibility of the luminous powder in the final product will be better.
Glow Technology recently developed a new luminous powder-it is effective enough to alleviate the problem of blackening in injection molding. It is the luminous powder for injection molding.
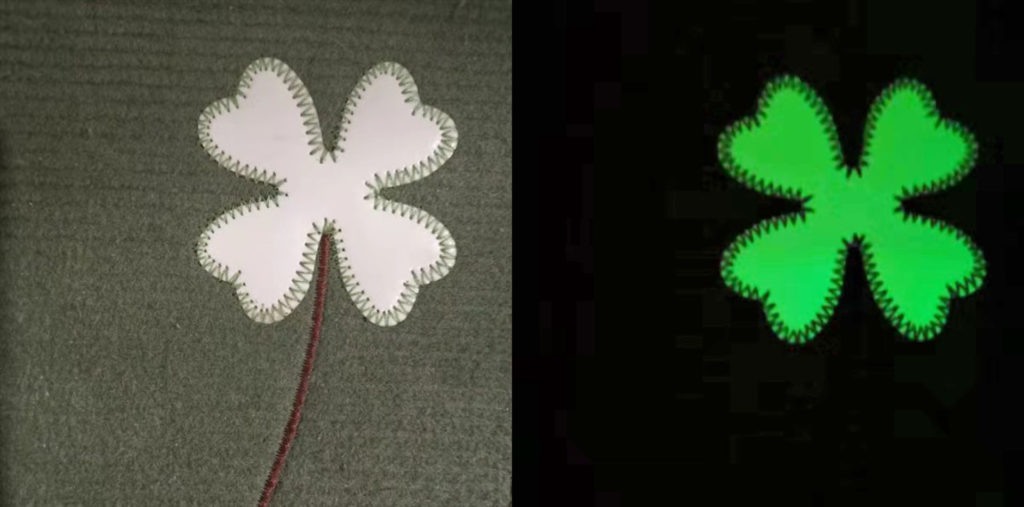
However, many producers only produce regular plastic not glow in the dark plastic but are still disturbed by the problem of black injection molding.
There are so many sources of blackening in injection molding, how to find out the culprit causing black spots?
CAUSES AND SOLUTIONS OF BLACK SPOTS IN PLASTIC INJECTION PRODUCTS
Ⅰ. MOLD
◆ Full pre-degreasing inspection can effectively prevent oily and rusty products and runners from being mixed into the crushed material and used (especially during the production process rather than during the initial trial);
◆ The gates of the mold are too small or rough, which will generate a lot of frictional heat. If the mold exhaust is not good, it will cause visible black stripes (black spots) in the gas combustion;
Ⅱ. EQUIPMENT:
Ⅱ. EQUIPMENT:
◆ The dryer motor runs for a long time. It will produce a lot of dust in the places you can’t see. You must clean it regularly;
◆ The filter screen of the dryer must also be cleaned and replaced regularly. Otherwise, it will enter the foreign body or the material will change color and agglomerate due to poor ventilation;
◆ Drying machine is not (entirely) sealed due to the negligence of operators or insufficient operating equipment, which causes dust in the air to enter; or dust is scattered and pollutes the surrounding products and materials in the grinder; It is not easy to ignore factors such as dead angle (conveying pipe and its interface), which causes the barrel to be not wholly cleaned during the refueling process;
◆ Long-term production operation, 6S, and its protection are usually not done welll, and dust falls on the equipment, resulting in mixing;
◆ The shielding of the grinder is not in place, resulting in contamination and contamination of other materials;
◆ When using a grinder, try to isolate black from white;
◆ The nozzle hole diameter is too small, or the inner surface is rough, which will generate a lot of frictional heat. If the mold exhaust is not good, it will cause visible black streaks (black spots) in the gas combustion.
◆ When the barrel or rubber head is worn and cracked and bent, a part of the polymer is overheated to produce black streaks (dark spots);
◆ When the rubber ring part is worn, the advance of the melted glue cannot be smooth, and the phenomenon of squeezing will cause too much gas in the material tube. When the shot is smooth, black streaks will occur due to sharp friction;
◆ Tolerance of the outer diameter of the rubber ring and the gap between the cylinder wall is too small,
which causes the friction of the screw melt to produce a large amount of friction and heat to cause black streaks. Make the screw melt smoothly);
◆ The eccentricity of the screw and the material tube generates very frictional heat;
◆ The compression ratio of the screw is too large, the groove of the feed part is shallow, and the friction between the inner wall of the barrel and the raw material is large, which causes the raw material to overheat and decompose to produce black streaks (dark spots);
◆ The temperature is incorrect. The actual temperature of the heating plate and the thermometer are too large. The temperature of a particular section is too hot, which is not easy to intuitive. You need to check it with a measuring device.
◆ The dryer motor runs for a long time. It will produce a lot of dust in the places you can’t see. You must clean it regularly;
◆ The filter screen of the dryer must also be cleaned and replaced regularly. Otherwise, it will enter the foreign body or the material will change color and agglomerate due to poor ventilation;
◆ Drying machine is not (entirely) sealed due to the negligence of operators or insufficient operating equipment, which causes dust in the air to enter; or dust is scattered and pollutes the surrounding products and materials in the grinder; It is not easy to ignore factors such as dead angle (conveying pipe and its interface), which causes the barrel to be not wholly cleaned during the refueling process;
◆ Long-term production operation, 6S, and its protection are usually not done welll, and dust falls on the equipment, resulting in mixing;
◆ The shielding of the grinder is not in place, resulting in contamination and contamination of other materials;
◆ When using a grinder, try to isolate black from white;
◆ The nozzle hole diameter is too small, or the inner surface is rough, which will generate a lot of frictional heat. If the mold exhaust is not good, it will cause visible black streaks (black spots) in the gas combustion.
◆ When the barrel or rubber head is worn and cracked and bent, a part of the polymer is overheated to produce black streaks (dark spots);
◆ When the rubber ring part is worn, the advance of the melted glue cannot be smooth, and the phenomenon of squeezing will cause too much gas in the material tube. When the shot is smooth, black streaks will occur due to sharp friction;
◆ Tolerance of the outer diameter of the rubber ring and the gap between the cylinder wall is too small,
which causes the friction of the screw melt to produce a large amount of friction and heat to cause black streaks. Make the screw melt smoothly);
which causes the friction of the screw melt to produce a large amount of friction and heat to cause black streaks. Make the screw melt smoothly);
◆ The eccentricity of the screw and the material tube generates very frictional heat;
◆ The compression ratio of the screw is too large, the groove of the feed part is shallow, and the friction between the inner wall of the barrel and the raw material is large, which causes the raw material to overheat and decompose to produce black streaks (dark spots);
◆ The temperature is incorrect. The actual temperature of the heating plate and the thermometer are too large. The temperature of a particular section is too hot, which is not easy to intuitive. You need to check it with a measuring device.
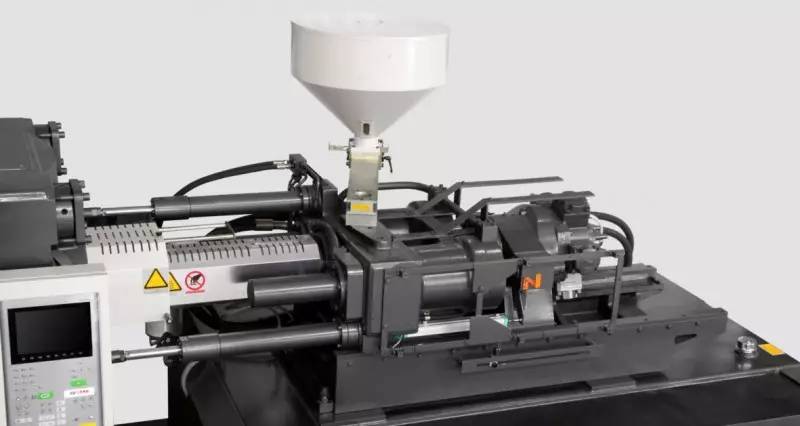
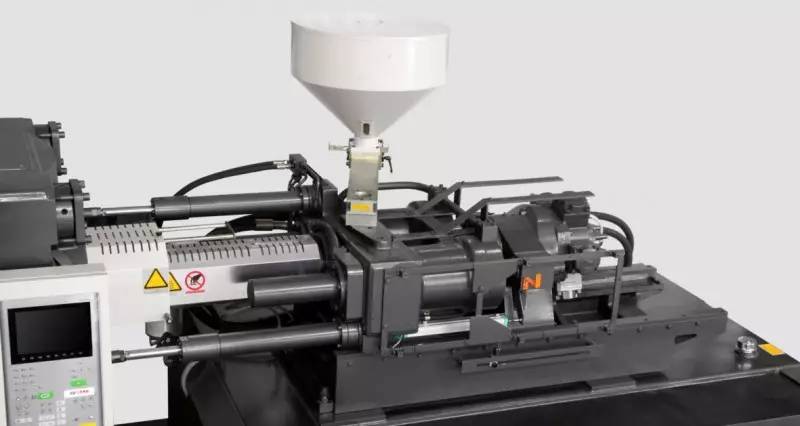
Ⅲ. OTHER:
◆ The production of different materials in the barrel for a long time, due to changes in temperature, oxidation, degradation, and the different adhesion of various materials to the metal surface, and other related factors, accumulated over time, resulting in screw surface, tube wall, nozzle, etc. In the beginning, a carbonized layer is gradually formed, and it is separated and brought out when it encounters materials with higher viscosity. In addition, if there are scars or gaps in the screw and tube wall, it will be easier for the molten material to stay and stop the startup Frequently, these problems will be exacerbated;
◆ People who do not understand the materials will crush the bad products, resulting in material confusion;
◆ The technician confirms the defective product whether it is crushed or discarded;
◆ When changing materials, it is convenient for the map operation. Only the air gun is used to blow away the remaining scraps, but this method cannot completely clean the barrel; or the air gun is used to bombard the scene, causing dust to diffuse throughout the workshop;
◆ The ground products or runner materials are directly inputted into the crusher;
◆ Bad products can be smashed by blowing with a wind gun casually;
◆ When processing the products in the red box, dump them directly into the crusher;
◆ When dealing with foreign matter, only one reason is found, and all the real reasons are found;
◆ The shredder has a scraper blade phenomenon, and the material is not adjusted and controlled in time;
◆ Stop method for unique materials such as PP, PMMA, ABS;
◆ The feeding method is wrong. If black material is added and white material is directly attached, black debris may fall into the white material due to static electricity or other reasons;
◆ The original low-temperature materials in the discharge pipe were not wholly replaced during washing. When the operating temperature increased, the low-temperature materials (fireproofing agents, additives, etc.)could not withstand this temperature and were degraded by heat. This usually occurs at the nozzle.(Especially during production and not during initial trials).
◆ The production of different materials in the barrel for a long time, due to changes in temperature, oxidation, degradation, and the different adhesion of various materials to the metal surface, and other related factors, accumulated over time, resulting in screw surface, tube wall, nozzle, etc. In the beginning, a carbonized layer is gradually formed, and it is separated and brought out when it encounters materials with higher viscosity. In addition, if there are scars or gaps in the screw and tube wall, it will be easier for the molten material to stay and stop the startup Frequently, these problems will be exacerbated;
◆ People who do not understand the materials will crush the bad products, resulting in material confusion;
◆ The technician confirms the defective product whether it is crushed or discarded;
◆ When changing materials, it is convenient for the map operation. Only the air gun is used to blow away the remaining scraps, but this method cannot completely clean the barrel; or the air gun is used to bombard the scene, causing dust to diffuse throughout the workshop;
◆ The ground products or runner materials are directly inputted into the crusher;
◆ Bad products can be smashed by blowing with a wind gun casually;
◆ When processing the products in the red box, dump them directly into the crusher;
◆ When dealing with foreign matter, only one reason is found, and all the real reasons are found;
◆ The shredder has a scraper blade phenomenon, and the material is not adjusted and controlled in time;
◆ Stop method for unique materials such as PP, PMMA, ABS;
◆ The feeding method is wrong. If black material is added and white material is directly attached, black debris may fall into the white material due to static electricity or other reasons;
◆ The original low-temperature materials in the discharge pipe were not wholly replaced during washing. When the operating temperature increased, the low-temperature materials (fireproofing agents, additives, etc.)could not withstand this temperature and were degraded by heat. This usually occurs at the nozzle.(Especially during production and not during initial trials).
Ⅳ. MATERIALS:
◆ The raw material has black dots, and the proportion of this black dot exceeds the allowable range of the customer’s incoming inspection or the permissible standard of the finished product;
◆ The raw material bag is damaged or contaminated during transportation, handling, and storage, and foreign matter is mixed in;
◆ Material is mixed with impurities during artificial proportioning or material making;
◆ Lubricants need to be added to some raw materials. If it is not added enough, frictional heat will be generated seriously, and too much exhaust gas will not be removed in time, which will cause black streaks (dark spots) in gas combustion;
◆ Insufficient heat resistance of the raw materials, which can not withstand the operating temperature of the raw materials (additives) to crack;
◆ The material bag or storage material bag is not clean. When it is used again, foreign matter will be mixed in.
The so-called black spots and black streaks in injection molding refer to the existence of black spots, stripes, or brown streaks on the production surface. However, the leading causes of black spots, black streaks, and brown streaks are the two aspects of material degradation and material pollution.
In the process of injection molding, improper degradation of materials will cause black spots, black streaks, and brown streaks in the finished product. These include the thermal decomposition of plastics, which can cause black spots, streaks, and brown streaks. If the plastic stays in the closed barrel and the surface of the screw for too long, it will cause carbonization and degradation, so black spots, stripes, or brown stripes will be generated during the injection molding process.
Material contamination will cause black spots, black streaks, or brown streaks in the injection-molded product. For example, the presence of dirty recycled materials, foreign materials, other colors of materials. Or low-molecular materials that are quickly dried and degraded in plastic can cause black spots, stripes, and brown stripes during the injection molding process. Secondly, the dust in the air also easily causes black spots on the surface of the workpiece.
In order to solve and avoid black spots, black streaks, and brown streaks during the injection molding process, the following precautions must be taken and taken.
Ⅰ. Material improvement method: Use non-polluting raw materials and place the material in a relatively closed storage bin to increase the thermal stability of the material.
Ⅱ. Mold design improvements: clean the ejector rod and slider, improve the exhaust system, clean and polish any dead corners in the runner to ensure that no build-up will occur, and clean the mold surface before injection.
Ⅲ. The injection molding machine improvement method: choose the appropriate injection molding machine tonnage, check the inner surface of the barrel, the screw surface is smooth, whether it will cause scratches accumulation.
Ⅳ. The production process conditions to improve methods: reduce the temperature of the barrel and nozzle, clean all aspects of the injection molding process, to avoid the black spots, black lines, brown stripes have been recycled.
Luminous powder for injection molding is a new product specially developed by our customers, which can effectively reduce the blackening problem of injection molding. I hope the above information will help you. Any questions, please feel free to contact us.
◆ The raw material has black dots, and the proportion of this black dot exceeds the allowable range of the customer’s incoming inspection or the permissible standard of the finished product;
◆ The raw material bag is damaged or contaminated during transportation, handling, and storage, and foreign matter is mixed in;
◆ Material is mixed with impurities during artificial proportioning or material making;
◆ Lubricants need to be added to some raw materials. If it is not added enough, frictional heat will be generated seriously, and too much exhaust gas will not be removed in time, which will cause black streaks (dark spots) in gas combustion;
◆ Insufficient heat resistance of the raw materials, which can not withstand the operating temperature of the raw materials (additives) to crack;
◆ The material bag or storage material bag is not clean. When it is used again, foreign matter will be mixed in.
The so-called black spots and black streaks in injection molding refer to the existence of black spots, stripes, or brown streaks on the production surface. However, the leading causes of black spots, black streaks, and brown streaks are the two aspects of material degradation and material pollution.
In the process of injection molding, improper degradation of materials will cause black spots, black streaks, and brown streaks in the finished product. These include the thermal decomposition of plastics, which can cause black spots, streaks, and brown streaks. If the plastic stays in the closed barrel and the surface of the screw for too long, it will cause carbonization and degradation, so black spots, stripes, or brown stripes will be generated during the injection molding process.
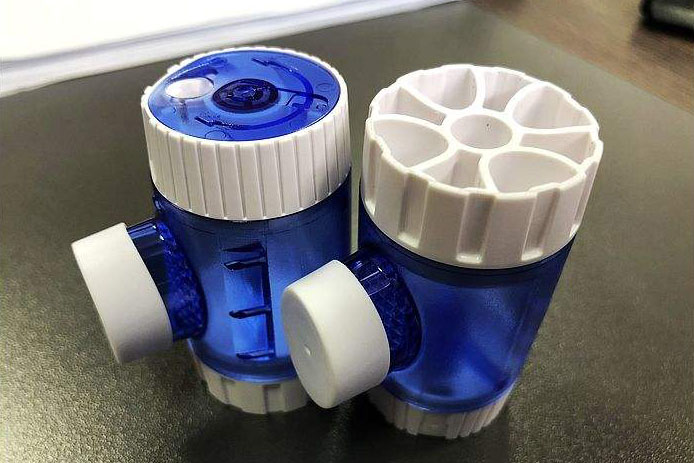
Material contamination will cause black spots, black streaks, or brown streaks in the injection-molded product. For example, the presence of dirty recycled materials, foreign materials, other colors of materials. Or low-molecular materials that are quickly dried and degraded in plastic can cause black spots, stripes, and brown stripes during the injection molding process. Secondly, the dust in the air also easily causes black spots on the surface of the workpiece.
In order to solve and avoid black spots, black streaks, and brown streaks during the injection molding process, the following precautions must be taken and taken.
Ⅰ. Material improvement method: Use non-polluting raw materials and place the material in a relatively closed storage bin to increase the thermal stability of the material.
Ⅱ. Mold design improvements: clean the ejector rod and slider, improve the exhaust system, clean and polish any dead corners in the runner to ensure that no build-up will occur, and clean the mold surface before injection.
Ⅲ. The injection molding machine improvement method: choose the appropriate injection molding machine tonnage, check the inner surface of the barrel, the screw surface is smooth, whether it will cause scratches accumulation.
Ⅳ. The production process conditions to improve methods: reduce the temperature of the barrel and nozzle, clean all aspects of the injection molding process, to avoid the black spots, black lines, brown stripes have been recycled.
Luminous powder for injection molding is a new product specially developed by our customers, which can effectively reduce the blackening problem of injection molding. I hope the above information will help you. Any questions, please feel free to contact us.
Comments
Post a Comment